Unwinder-Victoria
Victoria is a production line designed for the complete manufacturing of women's sanitary pads, encompassing the entire process from product creation to final packaging. The line is divided into several technological units:
Production Section – includes material unwinders, ensuring the continuous feeding of raw materials, as well as other process components such as cutting units, pad shaping, and product sorting.
Cutting and Sorting Section – handles precise cutting and quality control of individual pieces.
Packaging Section – ensures automated packaging of pads into individual wrappers and subsequently into boxes.
As part of our overhaul, we focused exclusively on the section of the line with the unwinders.
CUSTOMER REQUIRMENTS
- Overhaul of the distribution cabinet (wiring, protective elements, power supply, frequency inverters, PLC, inputs/outputs)
- Installation of new motors
- Replacement of motors, wiring, and motor connections
- Complete reprogramming of the unwinders
- Optimization of the entire unwinding process to enhance its reliability
BLOCK DIAGRAM
Picture 1. Control cabinet before reconfiguration Picture 2. Control cabinet after reconfiguration
ENGINE REPLACEMENT
As part of the modernization of the unwinders, the original two DC motors were replaced with new MCA14L35 servo motors with a power output of 3.9 kW. New cables were installed for the motors to ensure power supply, cooling (fan), and communication with the resolver.
Each cable was equipped with new industrial connectors, providing reliable electrical connections and increased resistance to vibrations and operating conditions. Once the cabling was completed, the servo motors were integrated into the control system, achieving full compatibility with the new control and enhanced precision in unwinder operation.
This upgrade significantly improved the dynamics, reliability, and efficiency of the entire equipment.
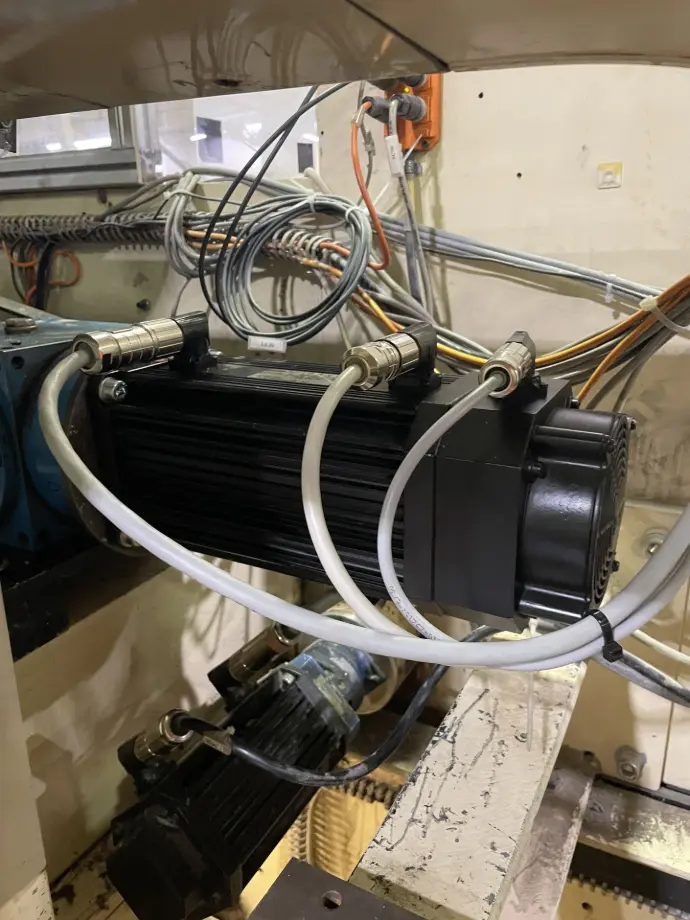
PROGRAMING
As part of the implementation of the new program, a comprehensive control system was designed and programmed for four motors, divided into two functional groups. The upper motors were optimized for handling film material, while the lower motors were tailored for processing textile-based material. Each group consisted of a pair of motors, ensuring uninterrupted operation during roll changes, thereby guaranteeing continuity of the production process.
Motor control was achieved using two dancers, which were responsible for precise tension regulation of the material. Additionally, the dancers provided material accumulation during transitional processes between rolls.
The programming included the creation of a web-based visualization accessible via mobile devices or PCs, enabling online monitoring and adjustment of key system parameters. This visualization also featured diagnostic functions, such as displaying alerts and fault conditions of the winders, significantly simplifying the identification and resolution of issues.
Following the introduction of the new program and hardware modernization, which included the replacement of motors, PLCs, and inverters, the system was optimized to achieve the full performance potential of the production line. The result is a more stable operation, reliable roll transitions, and a significant reduction in system susceptibility to faults. Overall, the functionality of the system has reached a higher level of efficiency and stability.