Complete Modernization of Palletizer with Lenze Automation for Bottled Water Line
We delivered a full-scale modernization of an industrial palletizer used in bottled water production. The project involved the complete overhaul of the control cabinet, installation of Lenze automation components, integration of safety systems from PILZ, and extensive PLC programming. The result: significantly faster palletizing cycles, improved safety, and seamless maintenance.
The palletizer is a flexible and compact solution for palletizing, designed for various industries. In this case, it is used for arranging and stacking water bottles.
CUSTOMER REQUIREMENTS
- Complete overhaul of the distribution cabinet (cabling, inverters, protection elements, power supplies, safety, the cabinet itself, PLC, inputs/outputs)
- Ovládací panel (HMI)
- Rewiring of all motors and sensors
- Replacement of safety elements (emergency stops, door locks, PILZ)
- Installation of a magnetostrictive sensor
- Kompletné preprogramovanie paletizačného zariadenia
- - Zrýchlenie celého procesu paletizácie
Preparation
Identification and procurement of all necessary components
Production
Manufacturing of the distribution cabinet, cabling...
Testing
Testing sensors, commissioning motors, PLC, invertors
Programming
Final programming, machine startup
BLOCK DIAGRAM
CONTROL CABINET
During the complete reconfiguration of the distribution cabinet, the original Allen-Bradley control system was replaced with a Lenze c520 PLC system. All input/output modules were upgraded to new Lenze components, ensuring compatibility and uniform integration of the control elements. Communication between different parts of the system is handled via the EtherCAT protocol. The original frequency inverters were replaced with new Lenze i700 models, which use a bus system, significantly streamlining installation. This system allows for power supply through a single source and the use of one protective device, minimizing the number of protective elements and simplifying the overall wiring.
A braking resistor was added to the inverters to eliminate the generation of unwanted voltage on the DC bus during braking. Safety elements were implemented using modules from PILZ, which manage the safety of door locks, barriers, and emergency stop buttons. The entire control cabinet is protected by an air conditioning unit mounted on the doors to prevent overheating of the equipment.
This technical approach significantly increased efficiency, enhanced safety, and simplified the management of the distribution cabinet.
Picture 1. Control cabinet before reconfiguration Picture 2. Control cabinet after reconfiguration
CONTROL PANEL
As part of the palletizer modernization, the control panel was completely redesigned and equipped with a 10-inch V450 HMI display from Lenze. This display was selected for its optimal size, ensuring easy operation of the equipment and excellent visibility of all necessary information. The modernization of the control panel also included an update to the software interface, enhancing the efficiency of operator interaction with the palletizer and improving response times for operations.
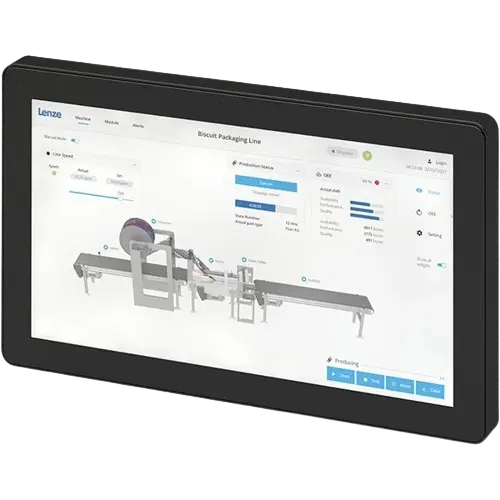
REWIRING MOTORS AND SESORS
As part of the overhaul, all power cables connected to the motors were completely replaced, including flexible cables housed in energy chains and fixed installations. The palletizer contained multiple sensors, for which multi-signal cables were replaced to ensure efficient transmission capacity and signal reliability. Additionally, the Motek motor controllers, which were previously integrated directly on the motors, were dismantled and relocated to the control cabinet. This optimized accessibility and simplified system maintenance.
PROGRAMING
The complete reprogramming of the palletizer was carried out using Lenze PLC3 Designer software. The programming was divided into several sections, including input and output conveyors, the elevator, the sheet placement spider, the stacking table, and the pallet feeder. Various software variants were developed for bottles with volumes of 0.5 L, 1.5 L, and 2 L. Each variant was optimized for different numbers of bottles and stacking layers. Additionally, a new stacking method was implemented to improve the visibility of logos on the packaging.
The primary goal of the palletizer reprogramming was to increase the overall efficiency of the process and ensure smoother transitions between operations. This was achieved by reducing time intervals between tasks, increasing operating speeds, and modifying the logic of certain operations.
A significant acceleration of the entire process was achieved by integrating a magnetostrictive sensor on the elevator, which enabled precise positioning during loading and unloading of bottles, even with the installed asynchronous motors. This sensor replaced the old inductive sensors, which often failed to detect the elevator's position, leading to the elevator overshooting the sensor and causing machine errors. With precise positioning, this issue was eliminated, allowing the elevator to achieve much higher speeds.
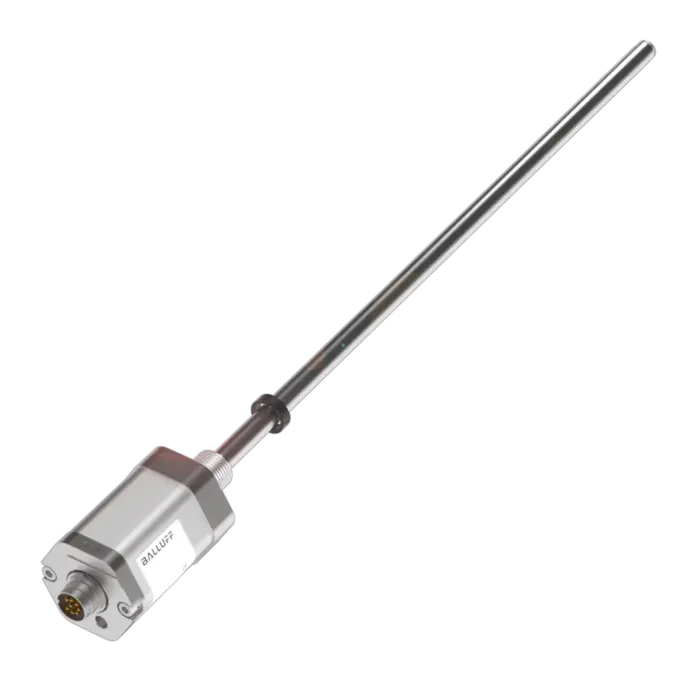
Before the modernization, the palletizer was prone to failures and did not reach the required operational speed. After the overhaul, the failure rate was reduced to almost zero, and there was an improvement in speed, diagnostics, and error resolution during servicing. The main benefit of this modernization is achieving operational speeds that are adequate for maximum production.
Let’s talk about how we can boost the performance of your production line.